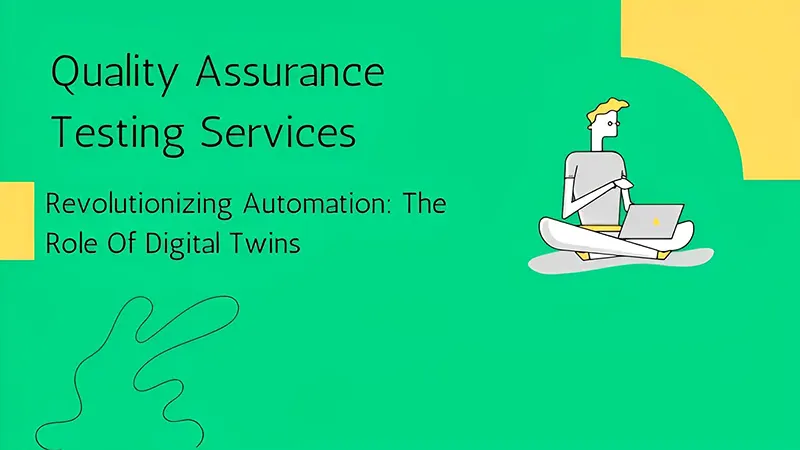
Digital twins are virtual representations of physical products, systems, or processes. They are created by merging computer-aided design models, sensor data, and other relevant information to construct a digital replica of the physical system.
This digital replica can then be used for monitoring, simulations, and analysis to optimize the performance of the physical system. The potential of digital twins goes beyond just manufacturing and can be employed for distinct quality assurance testing services automation applications.
The Role Of Digital Twins In Automation:
Digital twins can play a crucial role in automation by providing real-time data about the physical system. This data can be employed for various purposes, such as predicting failures, monitoring the system's performance, and optimizing its operation. By employing digital twins, firms can achieve greater efficiency and minimize costs.
Digital twins can be employed for automation in distinct industries, such as healthcare, transportation, manufacturing, and energy.
Let's take a closer look at how digital twins can be employed in these industries.
Manufacturing:
In manufacturing, digital twins can be implemented to optimize production processes, minimize downtime, and enhance product quality. By constructing a digital twin of the production line, manufacturers can monitor the system's performance and make adjustments in real-time to optimize its operation. It can result in enhanced efficiency, minimized costs, and improved product quality.
Digital twins can also be employed for predictive maintenance. By monitoring the system's performance, manufacturers can predict when a component will fail and schedule maintenance before it fails. It can minimize downtime and maintenance costs.
Healthcare:
In healthcare, digital twins can be employed to optimize patient care, enhance outcomes, and minimize costs.
By constructing a digital twin of a patient's body, doctors shall simulate distinct treatments and predict their outcomes. It can help doctors choose the ideal treatment for the patient and minimize the risk of complications.
Digital twins can also be employed for medical device development. By constructing a digital twin of a medical device, manufacturers can simulate the device's performance and make adjustments to optimize its operation. It can result in enhanced device performance and minimized costs.
Transportation:
Quality assurance testing services in transportation, digital twins shall be employed to optimize vehicle performance, eliminate maintenance costs, and boost safety.
By constructing a digital twin of a vehicle, manufacturers can monitor its performance and make amendments to optimize its operation. It can result in reduced maintenance costs, increased fuel efficiency, and improved safety.
Digital twins can also be used for traffic management. By constructing a digital twin of a road network, traffic managers can simulate different scenarios and predict traffic congestion. It can help traffic managers make informed decisions and reduce congestion.
Energy:
In the energy sector, digital twins can reduce downtime, optimize power generation, and improve safety. By creating a digital twin of a power plant, operators can monitor its performance and adjust to optimize its operation.
Digital twins can also be employed for predictive maintenance. By monitoring the system's performance, operators can predict when a component will fail and schedule maintenance before it fails. It can minimize downtime and maintenance costs.
The Perks Of Employing Digital Twins For Automation:
Digital twins are virtual representations of physical products, systems, or processes that offer countless perks when employed for automation.
By constructing digital twins, operators can monitor, analyze, and optimize physical systems in real-time, resulting in enhanced efficiency, minimized costs, and improved safety.
In this section, we will explore the perks of employing digital twins for automation.
Real-Time Monitoring:
One of the most significant perks of employing digital twins for automation is real-time monitoring. Digital twins provide operators with real-time data about the physical system, permitting them to monitor its performance and make adjustments in real-time. It can help prevent concerns before they occur and eliminate downtime.
For example, in a manufacturing plant, a digital twin of the production line shall be employed to monitor the performance of each machine in real-time. If a machine's performance seems to be degrading, the operator will be alerted and make adjustments to optimize its operation. It can help prevent breakdowns and minimize downtime, resulting in enhanced efficiency and productivity.
Predictive Maintenance:
Another significant perk is predictive maintenance. By monitoring the performance of a physical system, operators can predict when a component will fail and schedule maintenance before it fails. This can help lower downtime and maintenance costs.
For example, in a power plant, a digital twin of the turbines can be employed to monitor their performance. If a turbine's performance starts to degrade, the operator can be alerted, and maintenance can be scheduled before it fails. It can minimize downtime and maintenance costs, resulting in enhanced efficiency and productivity.
Optimization:
Using digital twins for automation can also help operators optimize the operation of physical systems. By analyzing the data from the digital twin, operators can detect inefficiencies and make adjustments to optimize the system's operation.
For example, in a transportation system, a digital twin of a vehicle can be implemented to monitor its performance. By analyzing the data, operators can detect areas where fuel efficiency can be improved and make adjustments to optimize the vehicle's operation. It can help reduce fuel costs and increase efficiency.
Simulation:
Digital twins can also be used for simulations, permitting operators to employ quality assurance testing services and predict outcomes. It can help operators make informed decisions and minimize the risk of problems occurring.
For example, in a healthcare setting, a digital twin of a patient's body can be employed to simulate different treatments and predict their outcomes. It can help doctors choose the best treatment for the patient and eliminate the risk of complications.
Conclusion:
In a nutshell, employing digital twins for automation offers countless perks, including real-time monitoring, optimization, predictive maintenance, and simulation. By employing digital twins, operators can monitor, analyze, and optimize physical systems in real-time, resulting in enhanced efficiency, minimized costs, and improved safety.
As digital twin technology continues to evolve, it is expected to become an increasingly important tool for automation in various industries.